Crystallization Kinetics of Polymers
Under certain conditions, polymers cooled from the melt can arrange into regular crystalline structures. The formation of these polymer crystals involves two processes that occur spontaneously when a polymer melt is cooled below its melting point. The first process is the formation of stable primary nuclei which itself are the result of fluctuations in density or order of supercooled melt. The growth rate of these nuclei requires sufficient mobility which increases with increasing temperature, whereas the rate of nucleation increases with decreasing temperature. Thus, the overall process displays a maximum growth rate somewhere between the melting point and glass transition temperature. Due to the larger rate of nucleation and smaller growth rate, the size of the crystallites (spherulites) decreases at lower temperatures whereas their number per unit volume increases. The lower mobility of the polymer chains at low temperatures also leads to less perfect crystallites (more defects in each lamellae).
Crystallizaton does not always occur, that is, some polymers are 100 percent amorphous. This is the case when the growth rate of the polymer crystallites is much slower than the cooling rate. Or in other words, crystallization only proceeds if the temperature stays in the appropriate temperature range for an extended time long enough to convert the melt into crystals. However, some portion of the polymer will always remain in a non-crystalline (irregular or amorphous) state. It's fraction will depend on factors such as cooling rate, molecular weight, and degree of branching.
In some cases, spontaneous nucleation is not sufficient to reach acceptable growth rates. In that case, small particles are added to the melt that act as seeds or nucleation agents. Partial melting can also improve the degree of crystallinity because the remaining crystals in the melt act as nuclei.
The growth rate as a function of temperature has more or less the shape of a bell curve with a maximum growth rate in between the glass transition and equilibrium melting temperature; starting from the melting point, as the temperature is lowered, the (spherulite) growth rate increases until it reaches a maximum at an intermediate temperature. Further decrease in temperature leads to a decrease in crystal growth rate and below the glass transition temperature it becomes virtually zero because molecular motion is too slow to allow for crystallization to take place.
The morphology of the crystals and and the degree of crystallinity depend on the type and structure of the polymer, and on the growth conditions. A narrow molecular weight distribution and a high molecular weight tend to increase the crystallinity. The same is true for strong intermolecular forces and stiff chain backbones because the molecules prefer an ordered arrangement with maximum packing density to maximize the number of secondary bonds. Bulky side groups and branching, on the other hand, lower the crystallinity because with increasing size of the side groups it becomes progressively more difficult for the polymer to fold and align itself along the crystal growth direction. The degree of crystallinity also depends on the tacticity of the polymer. The greater the order in a macromolecule the greater the likelihood of the molecule to undergo crystallization. In fact, most atactic polymers do not crystallize.
Generalized Avrami Equation
Isothermal crystallization is often described by the Avrami equation (1939):1,2
θc(t) = 1 - exp[-kn(T) tn]
Where θc(t) is the fraction of transformed material at time t, n is the Avrami exponent, and k the overall crystallization rate constant. The later parameter combines the contribution of both nucleation and growth.
The Avrami index in the equation above can be split into two indices:
n = nd + nn
where nd represents the dimensionality of the growing crystals. This parameter can only have the values 1,2, or 3. In the case of polymers, only 2 or 3 are encountered. nd = 2 describes two dimensional lamellar growth and nd = 3 three dimensional radial growth, i.e. spherulites. nn describes the time dependence of nucleation. This parameter has values between 0 and 1, where 0 corresponds to instantaneous nucleation an 1 to sporadic nucleation. A value of about 0.5 is often indicative for diffusion controlled growth, because diffusion is proportional to square root of time. Thus, the overall Avrami index, n, typically varies between 2 and 4.
In practice, the Avrami equation is normally written in its logarithmic form:
ln{-ln[1 - θc(t)]} = ln Q = ln kn + n ln t
A plot of ln Q versus ln t yields a straight line from which the Avrami parameters kn (antilog of intercept) and n (slope) can be readily extracted.
Crystallization Kinetik According to Avrami Model
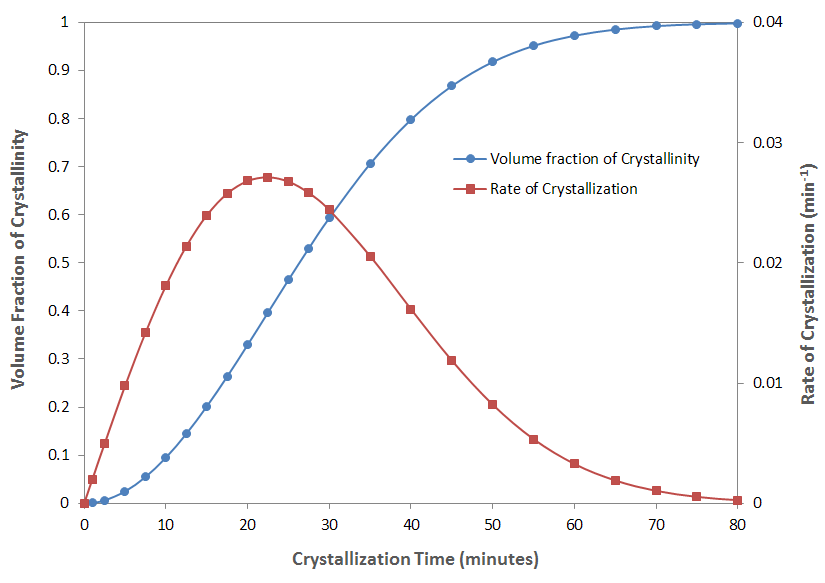
The figure above shows the normalized volume fraction of crystallinity and the rate of crystallization as a function of time for two dimensional growth kinetic (n = 2) and constant crystallization rate (k = 10-3 min.-2). The volume fraction has been normalized with the maximum possible crystallinity at infinite time and the rate of crystallization is the derivative of the Avrami equation with respect to time:
dθc(t) / dt = n tn-1 kn(T) exp[-kn(T) tn]
The crystallization half-time of this hypothetical crystal growth process is
t1/2 = [ln 2 / kn(T)]1/n = [ln 2 / 10-3]1/2 = 26.3 min.
and the maximum rate of crystallization is
tmax = [(n -1) / nkn(T)]1/n = [1 / 2·10-3]1/2 = 22.4 min.
References
M. Avrami, J. Chem. Phys., 7, 1103 (1939); J. Chem. Phys., 8, 212 (1940)
-
P. Supaphol, J.E Spruiell, J. of Appl. Polym. Sci., Vol. 75, 44-59 (2000)
P. Supaphol, N. Dangseeyun, P. Srimoaon, M. Nithitanakul Thermochimica Acta
406, 207-220 (2003)Cornelia Vasile, Handbook of Polyolefins, 2nd Ed., Marcel Dekker 2000